Un sistema computacional que puede optimizar la producción de las plantas eléctricas
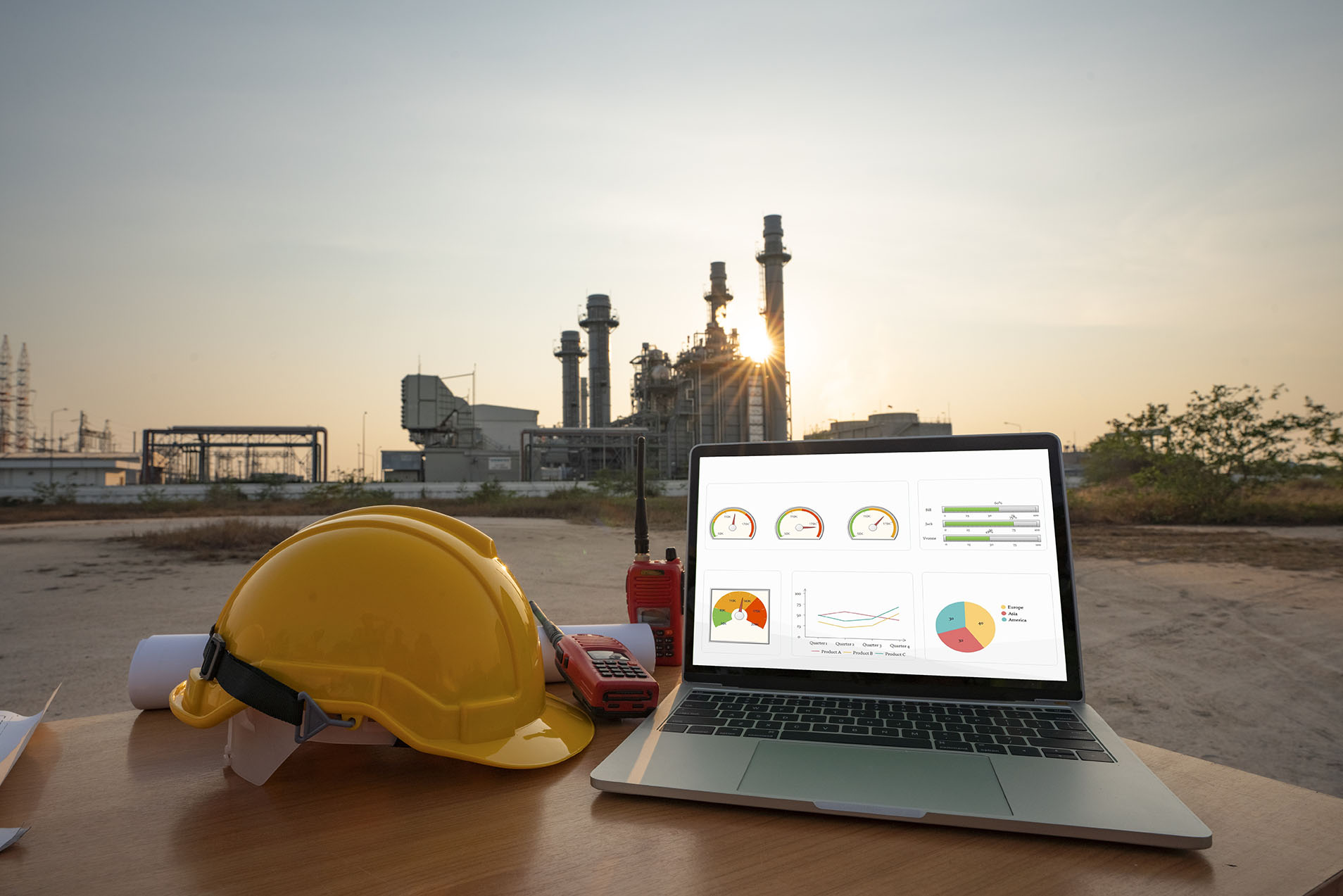
Por Rafael Batres, Erik Rosado, Emilio Garduño, Miguel Ángel Zúñiga
Artículo de divulgación científica
En los sistemas de generación de electricidad, uno de los retos más frecuentes es lograr mantener una operación balanceada entre el suministro y la demanda de electricidad (Kirby, 2007). Dicho balance es particularmente importante porque si se produce demasiada o muy poca energía, puede cambiar el punto de operación del generador y cambiar la frecuencia de la red eléctrica de suministro, que en México es de 60Hz. Estos cambios de frecuencia pueden dañar los aparatos eléctricos o incluso ocasionar un apagón.
Dado que la demanda de energía no es constante, una planta de generación de electricidad está diseñada para ajustar su producción de electricidad a los cambios de dicha demanda, y estos cambios no pueden ajustarse de manera instantánea. La demanda de electricidad cambia por algunos factores, como son los consumos eléctricos de acuerdo a las actividades de las personas e industrias, así como por las condiciones meteorológicas. A medida que se incrementen las plantas de generación renovable, se aumentan los niveles de variabilidad en la producción de electricidad[1].
Esta variabilidad estará siempre presente en algunas fuentes alternas de energía como son la energía solar y eólica, en donde su generación de energía eléctrica no es constante. Por ejemplo, la energía solar no tiene producción en la noche y la eólica podría ser afectada por cambios meteorológicos. Dicha variabilidad provoca que las operaciones de las plantas de generación tradicionales sean más complejas, debido a que dichas plantas se ven en la necesidad de proporcionar la cantidad de electricidad faltante cuando las energías renovables variables no pueden satisfacer la demanda. Esto puede ocurrir en diferentes intervalos dentro de un día, lo que requiere tener una estrategia para cumplir con estas demandas en tiempo real en los generadores convencionales.
Dentro de las tecnologías tradicionales para generación de electricidad, las plantas de ciclo combinado que combinan turbinas de gas y vapor tienen la habilidad de adaptar el suministro a través de una menor o mayor producción de electricidad (reducción o aumento de carga), así como arranques y paros. Para controlar los cambios de carga y los arranques o paros, una planta de ciclo combinado debe cambiar las temperaturas y presiones a través de la operación de varias válvulas que cambian los niveles de flujo de vapor, agua y gas. Aquí se presentan varios retos: ¿en qué orden se operan las válvulas? ¿Qué tan abiertas o cerradas deberán estar? ¿por cuánto tiempo deberán permanecer en cada posición de apertura?
Los cambios en temperaturas y presiones van de un estado inicial a un estado meta y pueden ocurrir de manera rápida o lenta. Lo ideal es llegar al estado meta en el menor tiempo posible. Sin embargo, los cambios súbitos en temperaturas y presiones pueden generar grandes niveles del llamado “estrés” en los componentes de la planta de generación, reduciendo el tiempo de vida útil de estos últimos. Esto es similar a llevar a un automóvil sedan de cero km/h a una velocidad de 200 km/h en un tiempo de 2 segundos. Si presionamos el pedal del acelerador hasta el fondo, podríamos lograr la velocidad deseada, pero si lo pisamos de manera gradual, tardaremos más para llegar esa velocidad. Ahora bien, podemos acelerar hasta el fondo, pero esto hará que el motor del automóvil se deteriore mucho más rápidamente (no sería raro que tiempo después aparecieran fugas de líquido u otros problemas mecánicos de manera prematura). La operación de las válvulas es análoga a la operación del acelerador. Las temperaturas y presiones son análogas a la velocidad. Queremos llegar al estado meta, pero cuidando la integridad de los componentes. Esto nos lleva a un reto más: ¿cómo operar las válvulas de la planta de generación de electricidad para llevar las temperaturas y presiones del estado inicial al estado meta, cuidando de afectar lo menos posible la vida útil de los componentes de planta?
Un nuevo sistema computacional
Para responder a los retos antes mencionados, se diseñó un novedoso sistema computacional que combina un modelo de simulación con un algoritmo de optimización. El modelo de simulación representa el comportamiento de la planta real de forma que las operaciones de las válvulas reflejen cambios en las temperaturas y presiones en varias partes de la planta. Dicho modelo está basado en ecuaciones matemáticas. Para comprobar que el modelo de la planta simulado es correcto, se validó por medio de la comparación con datos publicados en la literatura científica.
Para la implantación del modelo se utilizó el ambiente OpenModelica que permite el desarrollo de simuladores dinámicos. OpenModelica posee algoritmos para la resolución de sistemas de ecuaciones diferenciales, logrando que se puedan observar cambios en las variables con respecto al tiempo, lo que se conoce como simulación dinámica. La simulación dinámica es importante para los retos antes mencionados porque después de cambiar las posiciones de las válvulas, los efectos en las temperaturas y presiones no son instantáneos, sino que se evalúan a lo largo del tiempo. Esto es similar a controlar la temperatura del agua de la ducha con la válvula de agua caliente. Nos damos cuenta de que existe un retraso entre el momento en el que abrimos o cerramos la válvula y el cambio en la temperatura del agua. Adicionalmente, existe una interacción compleja entre las temperaturas, presiones y cambios de válvulas en distintas partes de la planta, haciendo que la predicción de cambios no sea trivial[2]. En resumen, el simulador dinámico permite predecir de manera fiel y precisa los cambios en las variables con respecto al tiempo. El modelo puede representar una simulación para una secuencia de operaciones de válvulas dado. Cada operación de válvula en la secuencia se definió como un conjunto de posiciones de válvulas y un tiempo durante el cual dichas posiciones permanecen fijas.
El otro elemento del sistema computacional es el algoritmo de optimización. Optimización se refiere al proceso para encontrar la mejor solución de un determinado problema, ya sea de manera global o local. El problema de optimización que concierne aquí consiste en encontrar la secuencia de operaciones de válvulas que permita llevar las temperaturas y presiones del estado inicial al final, cuidando de afectar lo menos posible la vida útil de los componentes de planta. Dado que las posiciones posibles de las válvulas se proponen de antemano y se trata de determinar qué operaciones se realizan y cuál es la mejor secuencia de estas, el problema de optimización es de tipo combinatorio. En otras palabras, el conjunto de soluciones al problema de optimización es finito, aunque dicho conjunto de soluciones es demasiado grande como para buscar la solución óptima de forma exhaustiva.
Afortunadamente, existen algoritmos que permiten aproximarse a la solución óptima con poco esfuerzo computacional: los algoritmos metaheurísticos. Estos algoritmos son métodos iterativos basados en una heurística que los guía para explorar los diferentes espacios de búsqueda, ademas de emplear la exploración, que permite ir mejorando las soluciones encontradas. Varios algoritmos metaheurísticos están inspirados en la naturaleza. Por ejemplo, los algoritmos genéticos utilizan poblaciones de individuos (soluciones) y están basados en la sobrevivencia del individuo más apto de acuerdo a la teoría evolutiva de Darwin, estos algoritmos pueden tener las siguientes operaciones: selección, cruzamiento, y mutación.
Asociado al reto de cuidar la vida útil de los componentes de planta está la predicción de esfuerzos termo-mecánicos. Para ello, también se usan modelos, los cuales van de modelos aproximados a modelos rigurosos. Los modelos aproximados tienen una menor precisión, aunque permiten cálculos más rápidos. Los modelos rigurosos son más precisos, pero toman más tiempo en resolverse dado que están formados por sistemas de ecuaciones diferenciales parciales. Por ejemplo, el cálculo de los esfuerzos de un sobrecalentador ocupa alrededor de tres horas en una computadora con un procesador central de 2.2 GHz y 8 MB de memoria. Suponiendo que el problema de optimización de la síntesis del perfil operativo se resuelve a través de 1,000 iteraciones ¡todo el proceso de optimización requeriría más de 500 días para completarse! ¡Un reto más!
El experimento
Para evaluar el sistema computacional, se propuso encontrar la secuencia óptima de válvulas de control que minimizara el tiempo necesario para el arranque y paro de una caldera de vapor, la cual es un componente importante en una planta de generación de electricidad. Los estados inicial y final se describen en términos de la presión interna y el flujo de vapor.
En este experimento se usó un algoritmo microgenético (GA) que se caracteriza por contener un número pequeño de individuos. Para evaluar cada individuo se propone una función que calcula qué tanto se acerca el sistema al estado meta y que tanto se desvía de las restricciones de esfuerzos termo-mecánicos. El algoritmo se integró al simulador de OpenModelica a través de una interface que permite el flujo bidireccional de información. Como resultado se obtuvo la secuencia óptima de operaciones de válvulas y se comparó con los resultados de un trabajo previo (Belkhir, 2015).
Para obtener un modelo de predicción de esfuerzos termo-mecánicos que fuera preciso y al mismo tiempo computacionalmente eficiente, se optó por desarrollar un modelo sustituto, es decir un modelo basado en el modelo riguroso, pero computacionalmente eficiente. La generación del modelo sustituto consistió en realizar diversas simulaciones con el modelo riguroso, variando presiones, temperaturas a lo largo del tiempo. Los resultados se utilizaron para generar un modelo de aprendizaje automático utilizando el método de redes neuronales artificiales[3]. Por ejemplo, el cálculo de los esfuerzos del sobrecalentador con el modelo sustituto toma alrededor de 7 segundos en vez de las 3 horas, usando el modelo riguroso, obteniendo una precisión similar.
Los hallazgos
Con esta investigación se demostró cómo se pueden encontrar secuencias óptimas de operación de válvulas que llevan a la planta de un estado inicial a uno final en menor tiempo, para poder ajustar la producción de electricidad de acuerdo a los cambios de demanda y a los cambios de generación de tipo solar o eólico.
Tal como se menciona en el artículo de investigación “A Framework for the Synthesis of Optimum Operating Profiles Based on Dynamic Simulation and a Micro Genetic Algorithm“, se logra llevar la planta al estado meta en un 35% del tiempo que toma la secuencia de operación de válvulas reportada en la literatura, tomando tan solo unos minutos en una computadora de tipo estación de trabajo.
Los autores
Rafael Batres es Doctor en Ingeniería de Sistemas. Es profesor investigador de la Escuela de Ingeniería y Ciencias del Tecnológico de Monterrey. Es miembro del Grupo de Innovación de Productos. Pertenece al Sistema Nacional de Investigadores, nivel 1. rafael.batres@tec.mx
Erik Rosado Tamariz es Maestro en Ingeniería Mecánica. Actualmente cursa el Doctorado en Ciencias de Ingeniería en la Escuela de Ingeniería y Ciencias del Tecnológico de Monterrey. A01652601@itesm.mx
Emilio Garduño Hernández es Ingeniero Industrial y de Sistemas, egresado del Tecnológico de Monterrey. Actualmente cursa la Maestría en Ciencias de la Ingeniería en la Escuela de Ingeniería y Ciencias del Tecnológico de Monterrey. A01128518@itesm.mx
Miguel Ángel Zúñiga García es Maestro en Ciencias de la Computación con especialidad en Inteligencia Artificial. Actualmente cursa el Doctorado en Ciencias de Ingeniería en la Escuela de Ingeniería y Ciencias del Tecnológico de Monterrey. A01745230@itesm.mx
¿Quieres saber más?
El artículo de investigación “Optimization of a drum boiler startup using dynamic simulation and a micro-genetic algorithm“, indizado recientemente en la base de datos Scopus, se puede encontrar en: https://doi.org/10.1016/j.egyr.2019.11.095
El artículo de investigación “A Framework for the Synthesis of Optimum Operating Profiles Based on Dynamic Simulation and a Micro Genetic Algorithm“, indizado recientemente en la base de datos Scopus, se puede encontrar en: https://doi.org/10.3390/en13030677
Referencias
- Kirby, B. (2007), Ancillary Services: Technical and Commercial Insights. [Online] Available at: http://www.consultkirby.com/files/Ancillary_Services_-_Technical_And_Commercial_Insights_EXT_.pdf.
- Erik Rosado-Tamariz, Miguel A. Zuniga-Garcia, Rafael Batres (2020) Optimization of a drum boiler startup using dynamic simulation and a micro-genetic algorithm, Energy Reports, 6, Supplement 2, pp. 410-416
- Rosado-Tamariz, Erik and Zuniga-Garcia, Miguel A. and Campos-Amezcua, Alfonso and Batres, Rafael (2020) A Framework for the Synthesis of Optimum Operating Profiles Based on Dynamic Simulation and a Micro Genetic Algorithm. Energies, 13, No. 3, pp. 1-23
[1] Esto es particularmente evidente en las fuentes de tipo solar y eólico, dado que la fuerza del viento no es constante y la luz solar cambia a lo largo del día.
[2] En el caso de la ducha no es lo mismo regular la temperatura del agua manteniendo la válvula del agua fría en una posición constante y operando la válvula de agua caliente que operar ambas válvulas simultáneamente.
[3] El método de redes neuronales artificiales está inspirado en las conexiones nerviosas del cerebro y se utiliza para solucionar problemas de predicción o clasificación de patrones.
Agradecimiento
Esta investigación es el resultado del Proyecto 266632 “Laboratorio Binacional para la Gestión Inteligente de la Sostenibilidad Energética y la Formación Tecnológica”, financiado por el Fondo SENER- CONACYT para la sostenibilidad energética (S0019201401).